Feature
HM520W Premium Flexible Mounter: with its best-in-class performance, the HM520W is a premium wide high-speed chip mounter that offers overwhelmingly excellent actual productivity, placement quality, applicability, and operational convenience.
Max. 26,000 CPH/Head
Best-in-Class Productivity
The industry-leading HM520W's cutting edge universal head and odd-shape head improves line productivity by maximizing efficiency with high actual productivity, wide applicability to components, wide head pitch, and simultaneous handing quantities.
In addition, the method of handing odd-shape components has been optimized to minimize the impact of cycle time due to deceleration.
High-speed and High-precision Placement of Odd-shape Components
The MF head can handle eight nozzles simultaneously, up to 14mm and T15mm components, and the improved component recognition motion and the avoidance of unnecessary Z-axis dceleration greatly reduce the placement cycle time of medium and large size components.
Enhanced Line Produictiivity
The wide type high speed chip mounter, HM520W, whose placement perfomance for odd-shape components is complemented, maximizes the line productivity of the HM series mounters along with the slim type high speed chip mounter, HM520Neo. which is advantageous for placing small chips.
PCB Tranfer Time Reduce by 47%
The PCB tranfer distance has been reduced by providing a buffer, and the PCB loading time can be significantly reduced since PCBs can be quickly detected and transferred by improving the sensor and belt.
Maintains Placement Accuracy through Automatic Calibration during Production
Possible to maintain placement accuracy continuously by performing major calibrations at the set time during production.
Automatic Nozzle Inspection and Cleaning during Production
Minimizes machine downtime due to a defective nozzle by checking for nozzle clogging and spring tension during production and by cleaning the nozzle with strong air blow when checking for any problem.
Suppression of Occurrence of Singgle Defect
The Vacuum Flow Monitoring sensor of the head defects the presence of components from component pickup to placement completion stage, preventing occurrence of a defect.
Automatic Calibration of Placement Coordinates (T-M2M-AC/SC)
Calibrates the placement offset of the chip mounter automatically to improve placement accuracy by receiving the fedback of the inspection results of the M-AOi in real time.
Detail Image
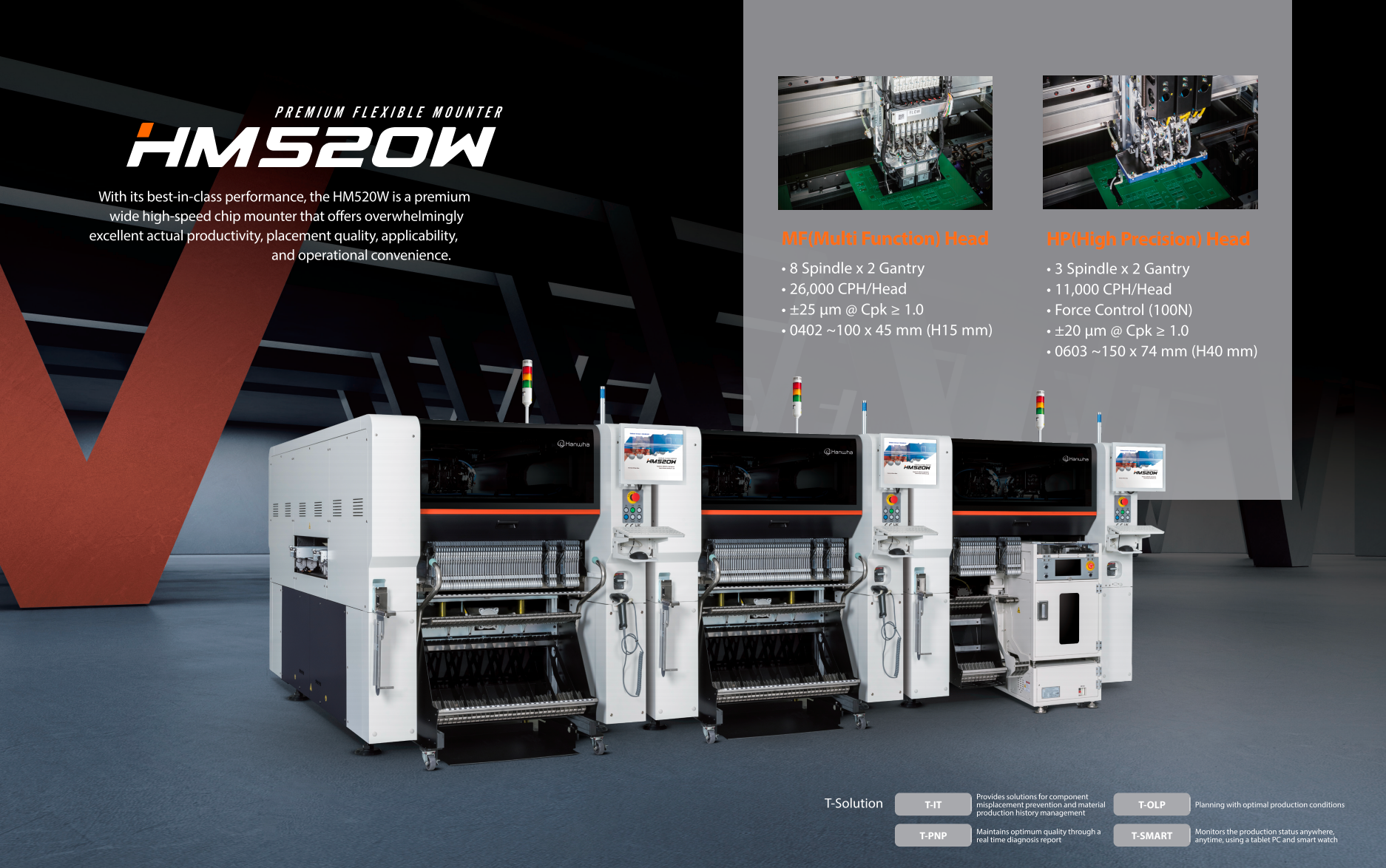
Specifications
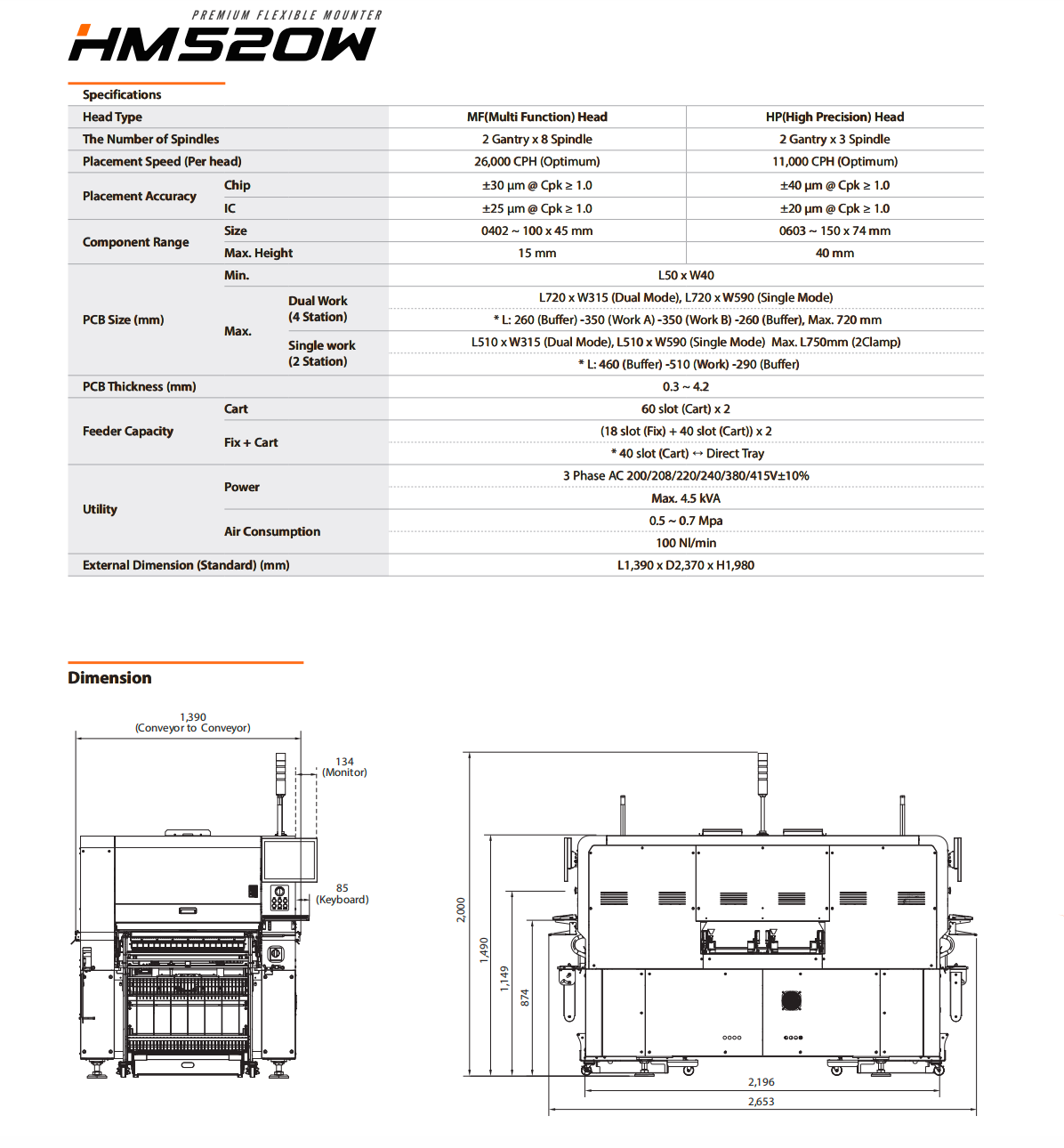
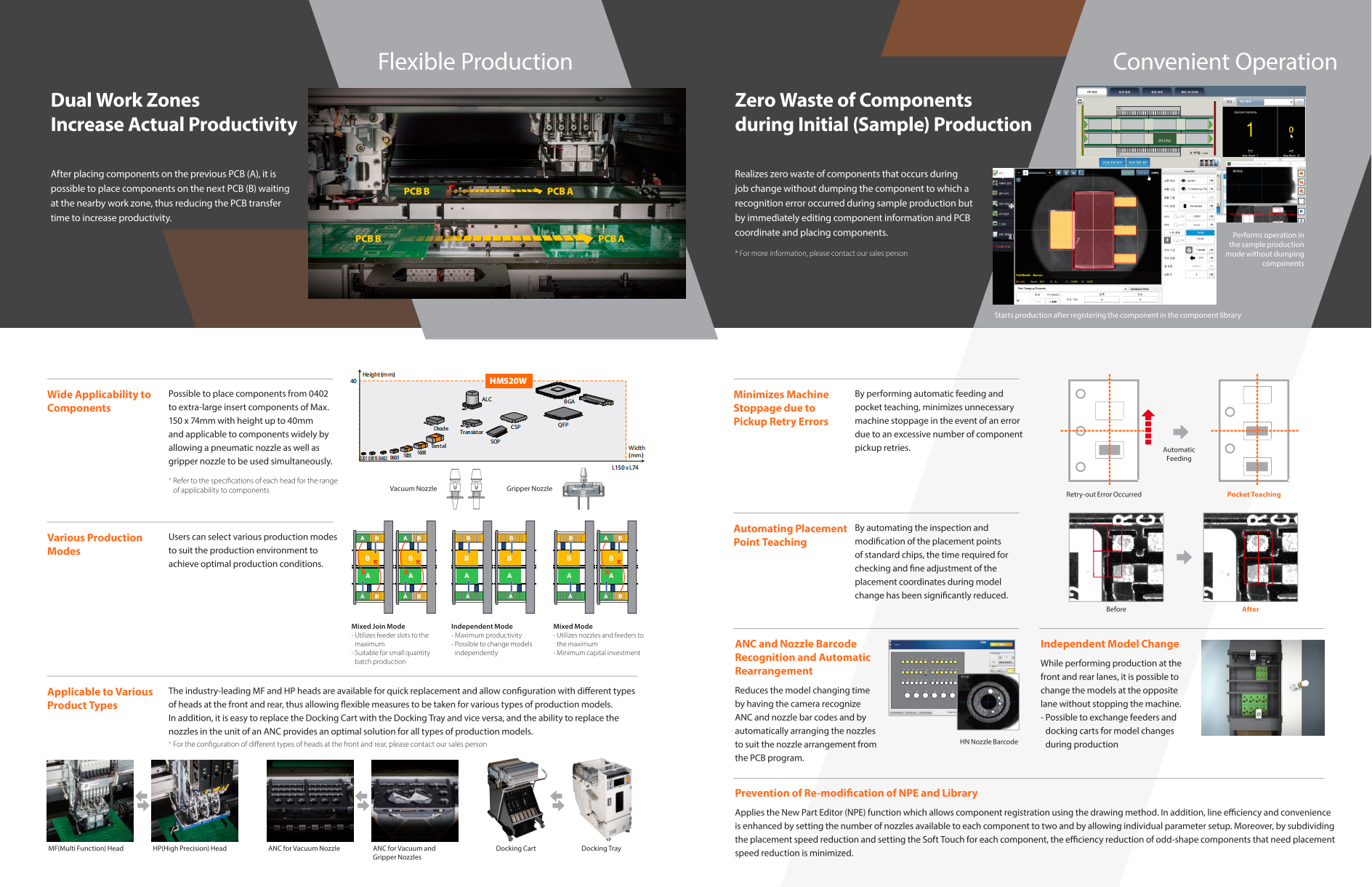