Feature
Hanwha XM520 is an equipment that can achieve the highest level of production capacity and quality among similar products, and has flexible product response capabilities.
A general-purpose machine with a wide range of optional functions and product line combinations. Through innovative functions, user convenience can be greatly improved and quick line changes can be achieved.
Through the wide bottom structure, not only can Stage Camera, Docking Cart, and Tray be used at the same time, but also the ability to cope with more types of components and flexible PCB correspondence capabilities can be achieved, thereby meeting the production line needs of customers with different needs.
Flexible Production
Extensive component support capabilities
Can mount 0201 microchips to Max. 55mm. L150mm components, and can handle components with a maximum height of 15mm
Diversified production models
Users can choose various production modes that suit the production environment to achieve optimal production conditions.
Various production lines can be formed through flexible PCB support capabilities
It can correspond to the maximum L1200 * 590mm PCB, which can realize the optimal production line combination that meets the user's production environment.
Using 2 Work Zones can increase actual production capacity
After PCB (A) is mounted, the next PCB (B) in the waiting area can be directly mounted, thus shortening the delivery time and increasing productivity.
Convenient Operation
The placement accuracy can be maintained through the automatic calibration function during the production process.
During the production process, placement accuracy is continuously maintained by performing major calibration work at set times.
Automatically inspect and clean nozzles during production
During the production process, check whether the nozzle is clogged and check the elasticity of the spring. If abnormalities are found, you can blow air through the nozzle to clean them, thus greatly reducing equipment shutdowns caused by defective nozzles.
No components are wasted when producing the first product
When a component identification error occurs during the production of the first article, the component information and PCB coordinates are immediately edited and mounted without discarding the component, thereby achieving zero waste of components during line change.
Automatic teaching placement point
Through automatic confirmation and modification of standard chip placement, the time for confirming placement coordinates and making fine adjustments during line change is greatly reduced.
Feeder setting unit
It comes standard with a feeder setting unit, which can be set in advance without stopping the equipment, thereby improving work efficiency.
Detail Image
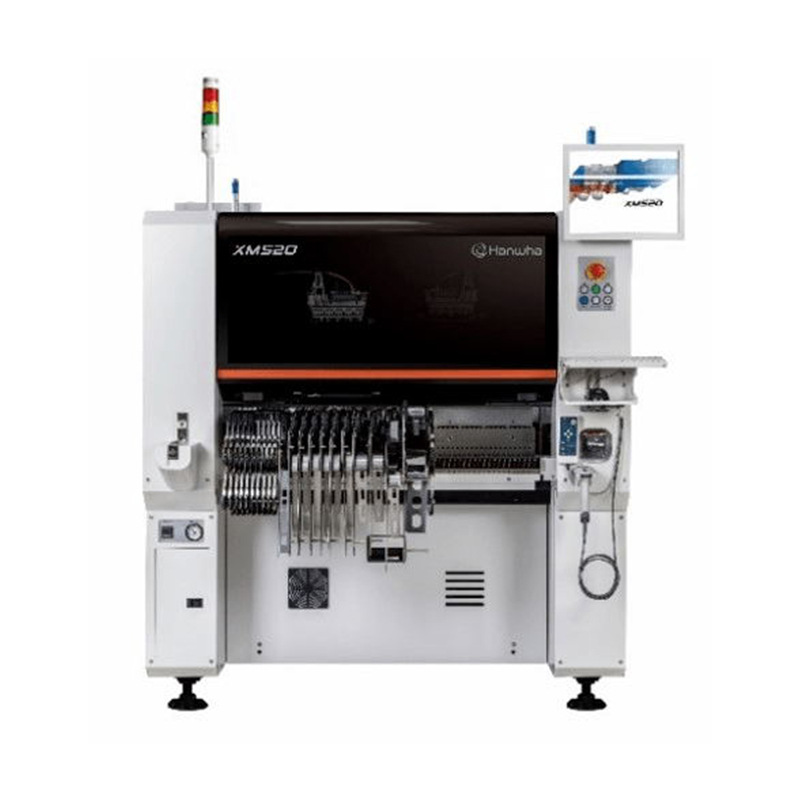
Specifications
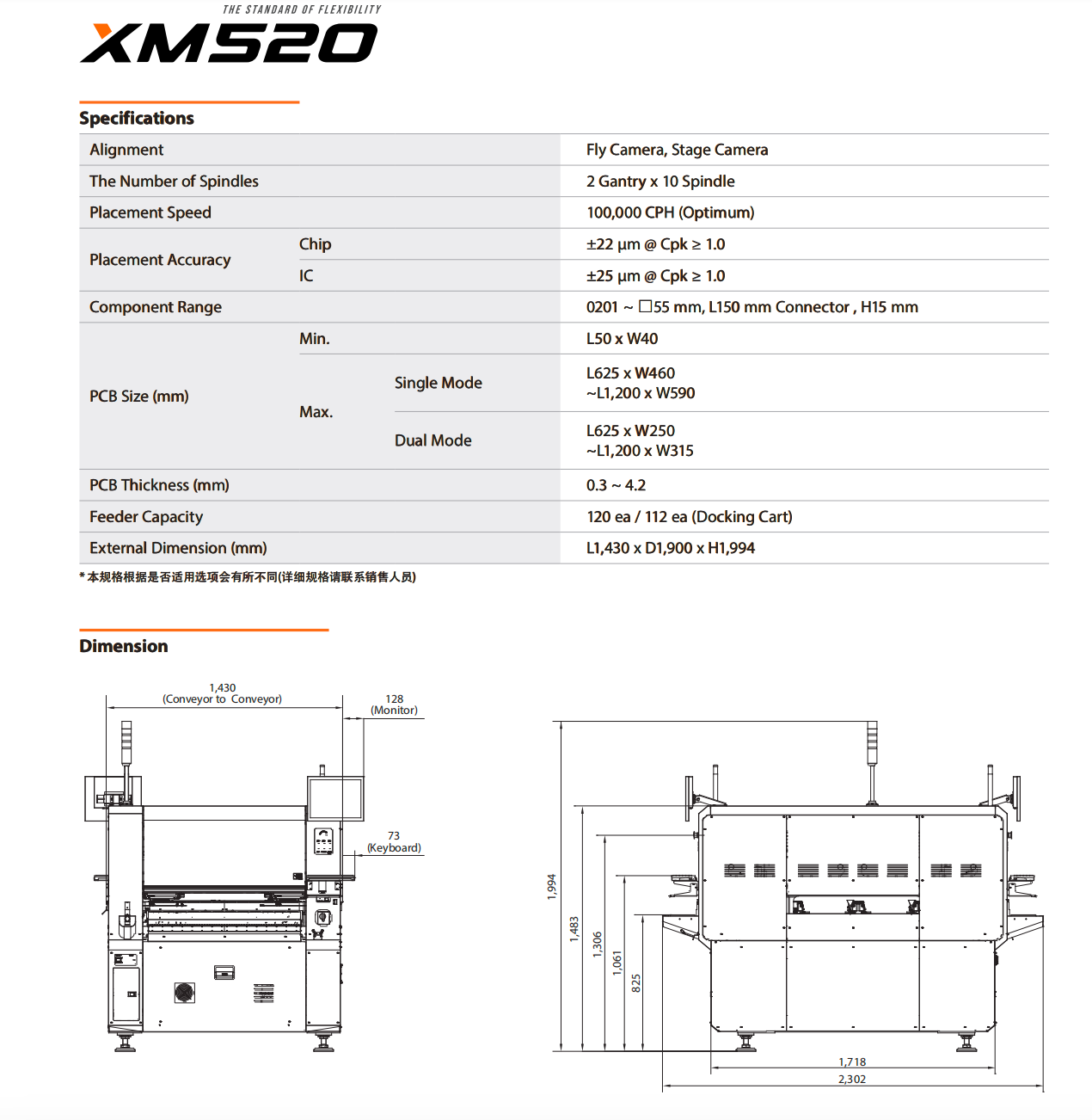