Пайка аплавленнем - гэта працэс, пры якім паяльная паста (ліпкая сумесь парашкападобнага прыпоя і флюсу) выкарыстоўваецца для часовага прымацавання аднаго або некалькіх электрычных кампанентаў да іх кантактных пляцовак, пасля чаго ўся зборка падвяргаецца кантраляванаму награванню, якое плавіць прыпой , пастаянна злучаючы сустаў.Нагрэў можна ажыццявіць шляхам прапускання вузла праз печ з аплавленнем або пад інфрачырвонай лямпай або шляхам паяння асобных злучэнняў алоўкам з гарачым паветрам.
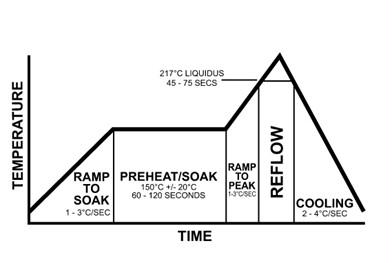
Пайка аплаўленнем з'яўляецца найбольш распаўсюджаным метадам мацавання кампанентаў павярхоўнага мантажу да друкаванай платы, хоць яе таксама можна выкарыстоўваць для кампанентаў са скразнымі адтулінамі, запаўняючы адтуліны паяльнай пастай і ўстаўляючы провады кампанентаў праз пасту.Паколькі пайка хваляй можа быць прасцейшай і таннейшай, аплавленне звычайна не выкарыстоўваецца на платах са скразнымі адтулінамі.Пры выкарыстанні на платах, якія змяшчаюць сумесь кампанентаў SMT і THT, аплаўленне праз адтуліны дазваляе выключыць этап паяння хваляй з працэсу зборкі, што патэнцыйна зніжае выдаткі на зборку.
Мэта працэсу аплавлення - расплавіць прыпой і нагрэць сумежныя паверхні без перагрэву і пашкоджання электрычных кампанентаў.У звычайным працэсе паяння аплавленнем звычайна ёсць чатыры стадыі, якія называюцца "зонамі", кожная з якіх мае асобны тэрмічны профіль: папярэдні нагрэў, тэрмічнае замочванне (часта скарачаецца да проста замочванне), аплаўленне і астуджэнне.
Зона папярэдняга нагрэву
Максімальны нахіл - гэта залежнасць тэмпературы ад часу, якая вымярае хуткасць змены тэмпературы на друкаванай плаце.Зона папярэдняга нагрэву часта з'яўляецца самай доўгай з зон і часта вызначае хуткасць нарошчвання.Хуткасць нарошчвання звычайна складае ад 1,0 °C да 3,0 °C у секунду, часта апускаючыся ад 2,0 °C да 3,0 °C (ад 4 °F да 5 °F) у секунду.Калі хуткасць перавышае максімальны нахіл, можа адбыцца пашкоджанне кампанентаў у выніку цеплавога ўдару або парэпання.
Паяльная паста таксама можа мець эфект распырсквання.Секцыя папярэдняга нагрэву - гэта месца, дзе растваральнік у пасце пачынае выпарацца, і калі хуткасць павышэння (або ўзровень тэмпературы) занадта нізкая, выпарэнне лятучых рэчываў флюсу будзе няпоўным.
Зона тэрмічнага замочвання
Другі раздзел, тэрмічнае замочванне, звычайна ўяўляе сабой уздзеянне ад 60 да 120 секунд для выдалення лятучых рэчываў паяльнай пасты і актывацыі флюсаў (гл. флюс), дзе кампаненты флюсу пачынаюць акісляльнае аднаўленне на высновах і пляцоўках кампанентаў.Занадта высокая тэмпература можа прывесці да распырсквання прыпоя або камякоў, а таксама да акіслення пасты, пляцовак мацавання і канчатковых частак кампанентаў.
Падобным чынам, патокі могуць не цалкам актывавацца, калі тэмпература занадта нізкая.У канцы зоны замочвання пажадана цеплавая раўнавага ўсёй зборкі непасрэдна перад зонай аплаўлення.Для памяншэння дэльта Т паміж кампанентамі рознага памеру або ў выпадку, калі друкаваная плата вельмі вялікая, прапануецца выкарыстоўваць профіль вытрымкі.Для памяншэння пустэч ва ўпакоўках плошчавага тыпу таксама рэкамендуецца прамочваць профіль.
Зона аплаўлення
Трэцяя секцыя, зона аплаўлення, таксама называецца «часам вышэй аплаўлення» або «часам вышэй ліквідусу» (TAL), і з'яўляецца часткай працэсу, дзе дасягаецца максімальная тэмпература.Важным фактарам з'яўляецца пікавая тэмпература, якая з'яўляецца максімальна дапушчальнай тэмпературай усяго працэсу.Звычайная пікавая тэмпература складае на 20–40 °C вышэй за ліквідус. Гэтая мяжа вызначаецца кампанентам зборкі з найменшай устойлівасцю да высокіх тэмператур (кампанент, найбольш успрымальны да тэрмічнага пашкоджання).Стандартная рэкамендацыя - адняць 5 °C ад максімальнай тэмпературы, якую можа вытрымліваць найбольш уразлівы кампанент, каб дасягнуць максімальнай тэмпературы для працэсу.Важна сачыць за тэмпературай працэсу, каб яна не перавышала гэты ліміт.
Акрамя таго, высокія тэмпературы (звыш 260 °C) могуць прывесці да пашкоджання ўнутраных плашчакоў кампанентаў SMT, а таксама спрыяць росту інтэрметалідаў.І наадварот, недастаткова высокая тэмпература можа перашкодзіць належнаму расцяканню пасты.
Час вышэй ліквідусу (TAL), або час вышэй аплаўлення, вымярае, як доўга прыпой знаходзіцца ў вадкасці.Флюс памяншае павярхоўнае нацяжэнне ў месцы злучэння металаў для дасягнення металургічнага злучэння, што дазваляе аб'ядноўваць асобныя сферы парашка прыпоя.Калі час профілю перавышае спецыфікацыі вытворцы, вынікам можа быць заўчасная актывацыя або расходаванне флюсу, эфектыўнае «высыханне» пасты перад адукацыяй паянага злучэння.Недастатковае суадносіны час/тэмпература прыводзіць да зніжэння ачышчальнага дзеяння флюсу, што прыводзіць да дрэннага змочвання, недастатковага выдалення растваральніка і флюсу і, магчыма, дэфекту паяных злучэнняў.
Эксперты звычайна рэкамендуюць самы кароткі TAL з магчымых, аднак большасць паст вызначае мінімальны TAL у 30 секунд, хоць, здаецца, няма дакладных прычын для гэтага канкрэтнага часу.Адной з магчымасцей з'яўляецца тое, што на друкаванай плаце ёсць месцы, якія не вымяраюцца падчас прафілявання, і, такім чынам, усталяванне мінімальна дапушчальнага часу ў 30 секунд зніжае верагоднасць таго, што невымераная вобласць не аплаўляецца.Высокі мінімальны час аплаўлення таксама забяспечвае запас трываласці ад перападаў тэмпературы печы.Час змочвання ў ідэале застаецца ніжэй за 60 секунд вышэй за ліквідус.Дадатковы час вышэй ліквідусу можа выклікаць празмерны рост інтэрметалідаў, што можа прывесці да далікатнасці злучэння.Плата і кампаненты таксама могуць быць пашкоджаныя праз працяглы час праз ліквідус, і большасць кампанентаў маюць дакладна абмежаваны час, на працягу якога яны могуць знаходзіцца пад уздзеяннем тэмператур, якія перавышаюць зададзены максімум.
Занадта мала часу вышэй ліквідусу можа захапіць растваральнікі і флюс і стварыць патэнцыял для халодных або тупых злучэнняў, а таксама пустэч пры пайцы.
Зона астуджэння
Апошняя зона - гэта зона астуджэння для паступовага астуджэння апрацаванай дошкі і зацвярдзення паяных злучэнняў.Правільнае астуджэнне прадухіляе залішняе адукацыю інтэрметалідаў або цеплавы шок кампанентаў.Тыповыя тэмпературы ў зоне астуджэння вагаюцца ад 30–100 °C (86–212 °F).Хуткая хуткасць астуджэння выбіраецца для стварэння дробназярністай структуры, якая найбольш механічна надзейная.
[1] У адрозненне ад максімальнай хуткасці нарошчвання, хуткасць паніжэння часта ігнаруецца.Можа быць, што хуткасць нарастання менш крытычная вышэй за пэўныя тэмпературы, аднак максімальна дапушчальны нахіл для любога кампанента павінен прымяняцца незалежна ад таго, награваецца ён ці астывае.Звычайна рэкамендуецца хуткасць астуджэння 4°C/с.Гэта параметр, які трэба ўлічваць пры аналізе вынікаў працэсу.
Тэрмін "аплавленне" выкарыстоўваецца для абазначэння тэмпературы, вышэй якой цвёрдая маса сплаву прыпоя напэўна расплавіцца (у адрозненне ад простага размякчэння).Пры астуджэнні ніжэй гэтай тэмпературы прыпой не будзе цячы.Разагрэты над ім яшчэ раз, прыпой будзе цячы зноў - такім чынам, "паўторнае цячэнне".
Сучасныя метады зборкі схем, якія выкарыстоўваюць пайку аплавленнем, не абавязкова дазваляюць прыпою цячы больш за адзін раз.Яны гарантуюць, што грануляваны прыпой, які змяшчаецца ў паяльнай пасце, перавышае тэмпературу аплаўлення прыпоя.
Цеплавое прафіляванне
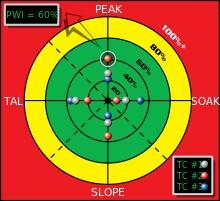
Графічнае прадстаўленне індэкса акна працэсу для цеплавога профілю.
У прамысловасці вытворчасці электронікі статыстычны паказчык, вядомы як індэкс акна працэсу (PWI), выкарыстоўваецца для колькаснай ацэнкі надзейнасці цеплавога працэсу.PWI дапамагае вымераць, наколькі добра працэс "упісваецца" ў вызначаны карыстальнікам ліміт працэсу, вядомы як ліміт спецыфікацыі. Кожны цеплавой профіль ацэньваецца ў залежнасці ад таго, як ён "упісваецца" ў акно працэсу (спецыфікацыя або мяжа допуску).
Цэнтр акна працэсу вызначаецца як нуль, а крайні край акна працэсу - як 99%. PWI, большы або роўны 100%, паказвае, што профіль не апрацоўвае прадукт у межах спецыфікацыі.PWI 99% паказвае, што профіль апрацоўвае прадукт у межах спецыфікацыі, але працуе на краі акна працэсу.PWI 60% паказвае, што профіль выкарыстоўвае 60% спецыфікацыі працэсу.Выкарыстоўваючы значэнні PWI, вытворцы могуць вызначыць, якую частку тэхналагічнага акна выкарыстоўвае пэўны цеплавы профіль.Больш нізкае значэнне PWI паказвае на больш надзейны профіль.
Для дасягнення максімальнай эфектыўнасці разлічваюцца асобныя значэнні PWI для працэсаў піка, нахілу, аплаўлення і вытрымкі цеплавога профілю.Каб пазбегнуць цеплавога ўдару, які ўплывае на выхад, трэба вызначыць і выраўнаваць самы круты ўхіл цеплавога профілю.Вытворцы выкарыстоўваюць спецыяльнае праграмнае забеспячэнне для дакладнага вызначэння і памяншэння крутасці схілу.Акрамя таго, праграмнае забеспячэнне таксама аўтаматычна перакалібруе значэнні PWI для працэсаў піка, нахілу, аплаўлення і замочвання.Усталёўваючы значэнні PWI, інжынеры могуць гарантаваць, што працэс паяння не пераграваецца і не астывае занадта хутка.
Час публікацыі: 1 сакавіка 2022 г