Le brasage par refusion est un processus dans lequel une pâte à souder (un mélange collant de poudre de soudure et de flux) est utilisée pour fixer temporairement un ou plusieurs composants électriques à leurs plages de contact, après quoi l'ensemble est soumis à une chaleur contrôlée, qui fait fondre la soudure. , reliant définitivement le joint.Le chauffage peut être réalisé en faisant passer l'assemblage dans un four à refusion ou sous une lampe infrarouge ou en soudant des joints individuels avec un crayon à air chaud.
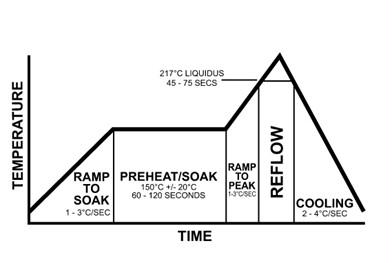
Le brasage par refusion est la méthode la plus courante pour fixer des composants montés en surface sur un circuit imprimé, bien qu'il puisse également être utilisé pour des composants traversants en remplissant les trous avec de la pâte à souder et en insérant les fils des composants à travers la pâte.Étant donné que le brasage à la vague peut être plus simple et moins cher, la refusion n'est généralement pas utilisée sur les cartes purement traversantes.Lorsqu'elle est utilisée sur des cartes contenant un mélange de composants SMT et THT, la refusion traversante permet d'éliminer l'étape de brasage à la vague du processus d'assemblage, ce qui réduit potentiellement les coûts d'assemblage.
Le but du processus de refusion est de faire fondre la soudure et de chauffer les surfaces adjacentes, sans surchauffer ni endommager les composants électriques.Dans le processus de brasage par refusion conventionnel, il y a généralement quatre étapes, appelées « zones », chacune ayant un profil thermique distinct : préchauffage, trempage thermique (souvent raccourci en simple trempage), refusion et refroidissement.
Zone de préchauffage
La pente maximale est une relation température/temps qui mesure la vitesse à laquelle la température sur le circuit imprimé change.La zone de préchauffage est souvent la plus longue des zones et établit souvent le taux de rampe.Le taux d'accélération se situe généralement entre 1,0 °C et 3,0 °C par seconde, se situant souvent entre 2,0 °C et 3,0 °C (4 °F à 5 °F) par seconde.Si le taux dépasse la pente maximale, des dommages aux composants dus à un choc thermique ou à des fissures peuvent survenir.
La pâte à souder peut également avoir un effet de projection.La section de préchauffage est l'endroit où le solvant de la pâte commence à s'évaporer, et si le taux de montée (ou le niveau de température) est trop faible, l'évaporation des matières volatiles du flux est incomplète.
Zone de trempage thermique
La deuxième section, le trempage thermique, est généralement une exposition de 60 à 120 secondes pour l'élimination des matières volatiles de la pâte à souder et l'activation des flux (voir flux), où les composants du flux commencent l'oxydoréduction sur les fils et les plages des composants.Une température trop élevée peut entraîner des projections ou des boules de soudure ainsi qu'une oxydation de la pâte, des plots de fixation et des terminaisons des composants.
De même, les flux peuvent ne pas s’activer complètement si la température est trop basse.A la fin de la zone de trempage, un équilibre thermique de l'ensemble de l'ensemble est souhaité juste avant la zone de refusion.Un profil de trempage est suggéré pour diminuer tout delta T entre des composants de différentes tailles ou si l'assemblage PCB est très grand.Un profil de trempage est également recommandé pour réduire les vides dans les emballages de type réseau.
Zone de refusion
La troisième section, la zone de refusion, est également appelée « temps au-dessus de la refusion » ou « temps au-dessus du liquidus » (TAL), et constitue la partie du processus où la température maximale est atteinte.Une considération importante est la température maximale, qui est la température maximale autorisée pour l’ensemble du processus.Une température maximale courante se situe entre 20 et 40 °C au-dessus du liquidus. Cette limite est déterminée par le composant de l'assemblage ayant la plus faible tolérance aux températures élevées (le composant le plus susceptible aux dommages thermiques).Une ligne directrice standard consiste à soustraire 5 °C à la température maximale que le composant le plus vulnérable peut supporter pour arriver à la température maximale du processus.Il est important de surveiller la température du processus pour l'empêcher de dépasser cette limite.
De plus, des températures élevées (au-delà de 260 °C) peuvent endommager les matrices internes des composants SMT et favoriser la croissance intermétallique.A l’inverse, une température pas assez élevée peut empêcher la pâte de refluer correctement.
Le temps au-dessus du liquidus (TAL), ou temps au-dessus de la refusion, mesure la durée pendant laquelle la soudure reste liquide.Le flux réduit la tension superficielle à la jonction des métaux pour réaliser une liaison métallurgique, permettant aux sphères individuelles de poudre de soudure de se combiner.Si le temps de profilage dépasse les spécifications du fabricant, il peut en résulter une activation ou une consommation prématurée du flux, « séchant » efficacement la pâte avant la formation du joint de soudure.Un rapport temps/température insuffisant entraîne une diminution de l'action nettoyante du flux, entraînant un mauvais mouillage, une élimination inadéquate du solvant et du flux et éventuellement des joints de soudure défectueux.
Les experts recommandent généralement le TAL le plus court possible, cependant, la plupart des pâtes spécifient un TAL minimum de 30 secondes, bien qu'il ne semble y avoir aucune raison claire pour cette durée spécifique.Une possibilité est qu'il y ait des endroits sur le PCB qui ne sont pas mesurés pendant le profilage, et par conséquent, définir le temps minimum autorisé à 30 secondes réduit les chances qu'une zone non mesurée ne reflue pas.Un temps de refusion minimum élevé offre également une marge de sécurité contre les changements de température du four.Le temps de mouillage reste idéalement inférieur à 60 secondes au dessus du liquidus.Un temps supplémentaire au-dessus du liquidus peut provoquer une croissance intermétallique excessive, ce qui peut conduire à une fragilité des joints.La carte et les composants peuvent également être endommagés pendant des périodes prolongées au cours du liquidus, et la plupart des composants ont une limite de temps bien définie pour la durée pendant laquelle ils peuvent être exposés à des températures supérieures à un maximum donné.
Un temps trop court au-dessus du liquidus peut piéger les solvants et le flux et créer un risque de joints froids ou ternes ainsi que de vides de soudure.
Zone de refroidissement
La dernière zone est une zone de refroidissement pour refroidir progressivement la carte traitée et solidifier les joints de soudure.Un refroidissement adéquat empêche la formation excessive d'intermétalliques ou les chocs thermiques sur les composants.Les températures typiques dans la zone de refroidissement varient de 30 à 100 °C (86 à 212 °F).Une vitesse de refroidissement rapide est choisie pour créer une structure à grains fins qui est la plus saine mécaniquement.
[1] Contrairement au taux de montée en puissance maximum, le taux de décélération est souvent ignoré.Il se peut que le taux de rampe soit moins critique au-dessus de certaines températures. Toutefois, la pente maximale autorisée pour tout composant doit s'appliquer, que le composant chauffe ou refroidisse.Une vitesse de refroidissement de 4°C/s est communément suggérée.C'est un paramètre à considérer lors de l'analyse des résultats du processus.
Le terme « refusion » est utilisé pour désigner la température au-dessus de laquelle une masse solide d'alliage de soudure est certaine de fondre (par opposition à simplement se ramollir).Si elle est refroidie en dessous de cette température, la soudure ne coulera pas.Réchauffée au-dessus une fois de plus, la soudure coulera à nouveau, d'où la « refusion ».
Les techniques modernes d'assemblage de circuits qui utilisent le brasage par refusion ne permettent pas nécessairement à la soudure de s'écouler plus d'une fois.Ils garantissent que la soudure granulée contenue dans la pâte à braser dépasse la température de refusion de la soudure concernée.
Profilage thermique
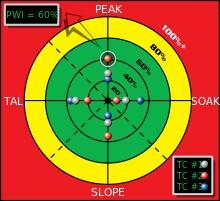
Une représentation graphique de l'index de fenêtre de processus pour un profil thermique.
Dans l'industrie de la fabrication électronique, une mesure statistique, connue sous le nom de Process Window Index (PWI), est utilisée pour quantifier la robustesse d'un processus thermique.PWI permet de mesurer dans quelle mesure un processus « s'intègre » dans une limite de processus définie par l'utilisateur, connue sous le nom de limite de spécification. Chaque profil thermique est classé en fonction de la manière dont il « s'intègre » dans une fenêtre de processus (la spécification ou la limite de tolérance).
Le centre de la fenêtre de processus est défini sur zéro et le bord extrême de la fenêtre de processus sur 99 %. Un PWI supérieur ou égal à 100 % indique que le profil ne traite pas le produit conformément aux spécifications.Un PWI de 99 % indique que le profil traite le produit conformément aux spécifications, mais s'exécute en bordure de la fenêtre de processus.Un PWI de 60 % indique qu'un profil utilise 60 % de la spécification du processus.En utilisant les valeurs PWI, les fabricants peuvent déterminer la part de la fenêtre de processus utilisée par un profil thermique particulier.Une valeur PWI inférieure indique un profil plus robuste.
Pour une efficacité maximale, des valeurs PWI distinctes sont calculées pour les processus de pointe, de pente, de refusion et de trempage d'un profil thermique.Pour éviter tout risque de choc thermique affectant le rendement, la pente la plus raide du profil thermique doit être déterminée et nivelée.Les fabricants utilisent un logiciel personnalisé pour déterminer et réduire avec précision l’inclinaison de la pente.De plus, le logiciel recalibre également automatiquement les valeurs PWI pour les processus de pointe, de pente, de refusion et de trempage.En définissant les valeurs PWI, les ingénieurs peuvent garantir que le travail de brasage par refusion ne surchauffe pas ou ne refroidit pas trop rapidement.
Heure de publication : 01 mars 2022