A soldagem por refluxo é um processo no qual uma pasta de solda (uma mistura pegajosa de solda em pó e fluxo) é usada para fixar temporariamente um ou vários componentes elétricos às suas almofadas de contato, após o que todo o conjunto é submetido a calor controlado, que derrete a solda. , conectando permanentemente a junta.O aquecimento pode ser realizado passando o conjunto através de um forno de refluxo ou sob uma lâmpada infravermelha ou soldando as juntas individuais com um lápis de ar quente.
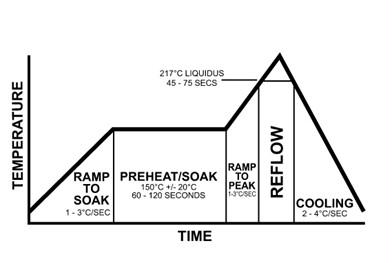
A soldagem por refluxo é o método mais comum de fixação de componentes de montagem em superfície a uma placa de circuito, embora também possa ser usada para componentes passantes, preenchendo os orifícios com pasta de solda e inserindo os terminais do componente através da pasta.Como a soldagem por onda pode ser mais simples e barata, o refluxo geralmente não é usado em placas puras.Quando usado em placas contendo uma mistura de componentes SMT e THT, o refluxo através do orifício permite que a etapa de soldagem por onda seja eliminada do processo de montagem, reduzindo potencialmente os custos de montagem.
O objetivo do processo de refluxo é derreter a solda e aquecer as superfícies adjacentes, sem superaquecer e danificar os componentes elétricos.No processo de soldagem por refluxo convencional, geralmente existem quatro estágios, chamados de "zonas", cada uma com um perfil térmico distinto: pré-aquecimento, imersão térmica (muitas vezes abreviada para apenas imersão), refluxo e resfriamento.
Zona de pré-aquecimento
A inclinação máxima é uma relação temperatura/tempo que mede a rapidez com que a temperatura na placa de circuito impresso muda.A zona de pré-aquecimento é frequentemente a mais longa das zonas e muitas vezes estabelece a taxa de rampa.A taxa de aceleração geralmente está em algum lugar entre 1,0 °C e 3,0 °C por segundo, geralmente caindo entre 2,0 °C e 3,0 °C (4 °F a 5 °F) por segundo.Se a taxa exceder a inclinação máxima, poderão ocorrer danos aos componentes por choque térmico ou rachaduras.
A pasta de solda também pode ter um efeito de respingos.A seção de pré-aquecimento é onde o solvente na pasta começa a evaporar e, se a taxa de aumento (ou nível de temperatura) for muito baixa, a evaporação dos voláteis do fluxo será incompleta.
Zona de imersão térmica
A segunda seção, imersão térmica, é normalmente uma exposição de 60 a 120 segundos para remoção de voláteis da pasta de solda e ativação dos fluxos (ver fluxo), onde os componentes do fluxo iniciam a redução da oxidação nos terminais e pastilhas dos componentes.Uma temperatura muito alta pode causar respingos ou bolinhas de solda, bem como oxidação da pasta, das almofadas de fixação e das terminações dos componentes.
Da mesma forma, os fluxos podem não ser totalmente ativados se a temperatura for muito baixa.No final da zona de imersão, é desejado um equilíbrio térmico de todo o conjunto, imediatamente antes da zona de refluxo.Sugere-se um perfil de imersão para diminuir qualquer delta T entre componentes de tamanhos variados ou se o conjunto da PCB for muito grande.Um perfil de imersão também é recomendado para diminuir a anulação em embalagens do tipo array de área.
Zona de refluxo
A terceira seção, a zona de refluxo, também é chamada de “tempo acima do refluxo” ou “tempo acima do liquidus” (TAL), e é a parte do processo onde a temperatura máxima é atingida.Uma consideração importante é a temperatura de pico, que é a temperatura máxima permitida de todo o processo.Uma temperatura de pico comum é 20–40 °C acima do liquidus. Este limite é determinado pelo componente no conjunto com a tolerância mais baixa para altas temperaturas (o componente mais suscetível a danos térmicos).Uma diretriz padrão é subtrair 5 °C da temperatura máxima que o componente mais vulnerável pode sustentar para chegar à temperatura máxima do processo.É importante monitorar a temperatura do processo para evitar que ultrapasse esse limite.
Além disso, altas temperaturas (acima de 260 °C) podem causar danos às matrizes internas dos componentes SMT, bem como promover o crescimento intermetálico.Por outro lado, uma temperatura que não seja suficientemente quente pode impedir que a pasta reflua adequadamente.
O tempo acima do liquidus (TAL), ou tempo acima do refluxo, mede por quanto tempo a solda permanece líquida.O fluxo reduz a tensão superficial na junção dos metais para realizar a ligação metalúrgica, permitindo que as esferas individuais de pó de solda se combinem.Se o tempo de perfil exceder a especificação do fabricante, o resultado poderá ser a ativação ou consumo prematuro do fluxo, “secando” efetivamente a pasta antes da formação da junta de solda.Uma relação tempo/temperatura insuficiente causa uma diminuição na ação de limpeza do fluxo, resultando em umedecimento deficiente, remoção inadequada do solvente e do fluxo e possivelmente juntas de solda defeituosas.
Os especialistas geralmente recomendam o TAL mais curto possível, no entanto, a maioria das pastas especifica um TAL mínimo de 30 segundos, embora pareça não haver uma razão clara para esse tempo específico.Uma possibilidade é que existam locais na PCB que não sejam medidos durante a criação de perfil e, portanto, definir o tempo mínimo permitido para 30 segundos reduz as chances de uma área não medida não refluir.Um tempo de refluxo mínimo elevado também proporciona uma margem de segurança contra mudanças de temperatura do forno.O tempo de umedecimento idealmente fica abaixo de 60 segundos acima do liquidus.O tempo adicional acima do liquidus pode causar crescimento intermetálico excessivo, o que pode levar à fragilidade das articulações.A placa e os componentes também podem ser danificados em períodos prolongados durante o liquidus, e a maioria dos componentes tem um limite de tempo bem definido para quanto tempo podem ficar expostos a temperaturas acima de um determinado máximo.
Muito pouco tempo acima do liquidus pode reter solventes e fluxo e criar o potencial para juntas frias ou cegas, bem como vazios de solda.
Zona de resfriamento
A última zona é uma zona de resfriamento para resfriar gradualmente a placa processada e solidificar as juntas de solda.O resfriamento adequado inibe a formação intermetálica excessiva ou choque térmico nos componentes.As temperaturas típicas na zona de resfriamento variam de 30–100 °C (86–212 °F).Uma taxa de resfriamento rápida é escolhida para criar uma estrutura de grão fino que seja mecanicamente mais sólida.
[1] Ao contrário da taxa máxima de aceleração, a taxa de desaceleração é frequentemente ignorada.Pode ser que a taxa de rampa seja menos crítica acima de certas temperaturas; no entanto, a inclinação máxima permitida para qualquer componente deve ser aplicada quer o componente esteja aquecendo ou esfriando.Uma taxa de resfriamento de 4°C/s é comumente sugerida.É um parâmetro a considerar na análise dos resultados do processo.
O termo "refluxo" é usado para se referir à temperatura acima da qual uma massa sólida de liga de solda derreterá (em vez de apenas amolecer).Se for resfriado abaixo desta temperatura, a solda não fluirá.Aquecida acima dela mais uma vez, a solda fluirá novamente - daí o "refluxo".
As técnicas modernas de montagem de circuitos que usam soldagem por refluxo não permitem necessariamente que a solda flua mais de uma vez.Eles garantem que a solda granulada contida na pasta de solda supere a temperatura de refluxo da solda envolvida.
Perfil térmico
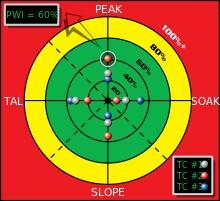
Uma representação gráfica do índice da janela de processo para um perfil térmico.
Na indústria de fabricação de eletrônicos, uma medida estatística conhecida como Índice de Janela de Processo (PWI) é usada para quantificar a robustez de um processo térmico.O PWI ajuda a medir o quão bem um processo "se ajusta" a um limite de processo definido pelo usuário, conhecido como Limite de Especificação. Cada perfil térmico é classificado de acordo com como ele "se ajusta" a uma janela de processo (a especificação ou limite de tolerância).
O centro da janela do processo é definido como zero e a borda extrema da janela do processo como 99%. Um PWI maior ou igual a 100% indica que o perfil não processa o produto dentro da especificação.Um PWI de 99% indica que o perfil processa o produto dentro das especificações, mas é executado na borda da janela de processo.Um PWI de 60% indica que um perfil utiliza 60% da especificação do processo.Ao usar valores PWI, os fabricantes podem determinar quanto da janela do processo um determinado perfil térmico utiliza.Um valor de PWI mais baixo indica um perfil mais robusto.
Para máxima eficiência, valores separados de PWI são calculados para processos de pico, inclinação, refluxo e absorção de um perfil térmico.Para evitar a possibilidade de choque térmico afetar a saída, a inclinação mais acentuada no perfil térmico deve ser determinada e nivelada.Os fabricantes usam software personalizado para determinar e diminuir com precisão a inclinação da encosta.Além disso, o software também recalibra automaticamente os valores PWI para os processos de pico, inclinação, refluxo e absorção.Ao definir os valores PWI, os engenheiros podem garantir que o trabalho de soldagem por refluxo não superaqueça ou esfrie muito rapidamente.
Horário da postagem: 01/03/2022