Yeniden akışlı lehimleme, bir veya daha fazla elektrik bileşenini kontak pedlerine geçici olarak bağlamak için bir lehim pastasının (toz halinde lehim ve akıdan oluşan yapışkan bir karışım) kullanıldığı, ardından tüm düzeneğin lehimi eriten kontrollü ısıya tabi tutulduğu bir işlemdir. , eklemi kalıcı olarak bağlar.Isıtma, düzeneğin bir yeniden akışlı fırından veya bir kızılötesi lambanın altından geçirilmesiyle veya tek tek bağlantı noktalarının sıcak hava kalemiyle lehimlenmesiyle gerçekleştirilebilir.
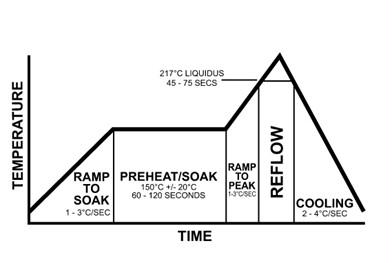
Yeniden akışlı lehimleme, yüzeye montaj bileşenlerini bir devre kartına bağlamanın en yaygın yöntemidir, ancak aynı zamanda deliklerin lehim macunu ile doldurulması ve bileşen uçlarının macunun içine yerleştirilmesi yoluyla açık delikli bileşenler için de kullanılabilir.Dalga lehimleme daha basit ve daha ucuz olabileceğinden, yeniden akış genellikle saf delikli levhalarda kullanılmaz.SMT ve THT bileşenlerinin bir karışımını içeren kartlarda kullanıldığında, delik içinden yeniden akış, dalga lehimleme adımının montaj sürecinden çıkarılmasına olanak tanır ve potansiyel olarak montaj maliyetlerini azaltır.
Yeniden akış işleminin amacı, lehimi eritmek ve bitişik yüzeyleri aşırı ısınmadan ve elektrikli bileşenlere zarar vermeden ısıtmaktır.Geleneksel yeniden akışlı lehimleme işleminde genellikle "bölgeler" olarak adlandırılan ve her biri farklı bir termal profile sahip olan dört aşama vardır: ön ısıtma, termal ıslatma (genellikle sadece ıslatma olarak kısaltılır), yeniden akış ve soğutma.
Ön ısıtma bölgesi
Maksimum eğim, baskılı devre kartı üzerindeki sıcaklığın ne kadar hızlı değiştiğini ölçen bir sıcaklık/zaman ilişkisidir.Ön ısıtma bölgesi genellikle bölgelerin en uzunudur ve sıklıkla rampa oranını belirler.Yükselme hızı genellikle saniyede 1,0 °C ile 3,0 °C arasındadır ve sıklıkla saniyede 2,0 °C ile 3,0 °C (4 °F ila 5 °F) arasına düşer.Hız maksimum eğimi aşarsa, termal şok veya çatlama nedeniyle bileşenlerde hasar meydana gelebilir.
Lehim pastasının da sıçrama etkisi olabilir.Ön ısıtma bölümü, macundaki solventin buharlaşmaya başladığı yerdir ve eğer yükselme hızı (veya sıcaklık seviyesi) çok düşükse, akı uçucularının buharlaşması tamamlanmaz.
Termal ıslatma bölgesi
İkinci bölüm olan termal ıslatma, lehim pastası uçucu maddelerinin uzaklaştırılması ve akı bileşenlerinin bileşen uçları ve pedler üzerinde oksit indirgemeye başladığı akıların (akıya bakınız) aktivasyonu için tipik olarak 60 ila 120 saniyelik bir maruz kalmadır.Çok yüksek bir sıcaklık, lehimin sıçramasına veya topaklaşmasına, ayrıca macunun, bağlantı pedlerinin ve bileşen uçlarının oksidasyonuna neden olabilir.
Benzer şekilde sıcaklık çok düşükse akışlar tam olarak etkinleşmeyebilir.Islatma bölgesinin sonunda, yeniden akış bölgesinin hemen öncesinde tüm düzeneğin termal dengesinin sağlanması arzu edilir.Farklı boyutlardaki bileşenler arasında veya PCB düzeneği çok büyükse herhangi bir delta T'yi azaltmak için bir emme profili önerilir.Alan dizisi tipi paketlerdeki boşlukları azaltmak için bir ıslatma profili de tavsiye edilir.
Yeniden akış bölgesi
Üçüncü bölüm olan yeniden akış bölgesi, aynı zamanda "yeniden akışın üzerindeki süre" veya "sıvılaşmanın üzerindeki süre" (TAL) olarak da anılır ve sürecin maksimum sıcaklığa ulaşılan kısmıdır.Önemli bir husus, tüm prosesin izin verilen maksimum sıcaklığı olan tepe sıcaklığıdır.Yaygın bir tepe sıcaklığı, sıvılaşmanın 20–40 °C üzerindedir. Bu sınır, montaj üzerindeki yüksek sıcaklıklara karşı en düşük toleransa sahip bileşen tarafından belirlenir (Termal hasara en duyarlı bileşen).Standart bir kılavuz, en hassas bileşenin işlem için maksimum sıcaklığa ulaşmak için dayanabileceği maksimum sıcaklıktan 5 °C çıkarmaktır.Bu sınırı aşmasını önlemek için proses sıcaklığının izlenmesi önemlidir.
Ek olarak, yüksek sıcaklıklar (260 °C'nin üzerinde) SMT bileşenlerinin iç kalıplarına zarar verebileceği gibi metaller arası büyümeyi de teşvik edebilir.Tersine, yeterince sıcak olmayan bir sıcaklık, macunun yeterince yeniden akmasını engelleyebilir.
Sıvılaşmanın üzerindeki süre (TAL) veya yeniden akışın üzerindeki süre, lehimin ne kadar süreyle sıvı kaldığını ölçer.Akı, metalurjik bağlanmayı gerçekleştirmek için metallerin birleşim yerindeki yüzey gerilimini azaltır ve bireysel lehim tozu kürelerinin birleşmesine olanak tanır.Profil süresi üreticinin spesifikasyonlarını aşarsa sonuç, lehim bağlantısının oluşmasından önce macunun etkili bir şekilde "kurutulması" nedeniyle erken eritken aktivasyonu veya tüketimi olabilir.Yetersiz bir zaman/sıcaklık ilişkisi, lehim pastasının temizleme etkisinde bir azalmaya neden olur, bu da zayıf ıslanmaya, solvent ve pastanın yetersiz uzaklaştırılmasına ve muhtemelen kusurlu lehim bağlantılarına neden olur.
Uzmanlar genellikle mümkün olan en kısa TAL'yi tavsiye eder, ancak çoğu macun minimum 30 saniyelik TAL belirtir, ancak bu belirli süre için net bir neden yok gibi görünmektedir.Bir olasılık, PCB üzerinde profil oluşturma sırasında ölçülmeyen yerlerin bulunmasıdır ve bu nedenle izin verilen minimum süreyi 30 saniyeye ayarlamak, ölçülmeyen bir alanın yeniden akmama olasılığını azaltır.Yüksek minimum yeniden akış süresi aynı zamanda fırın sıcaklığı değişikliklerine karşı bir güvenlik marjı sağlar.Islanma süresi ideal olarak sıvılaşma süresinin 60 saniyenin altında kalır.Liquidus'un üzerindeki ilave süre, aşırı intermetalik büyümeye neden olabilir ve bu da eklem kırılganlığına yol açabilir.Kart ve bileşenler aynı zamanda sıvılaşma nedeniyle uzun süreler boyunca hasar görebilir ve çoğu bileşenin, belirli bir maksimumun üzerindeki sıcaklıklara ne kadar süreyle maruz kalabilecekleri konusunda iyi tanımlanmış bir zaman sınırı vardır.
Sıvılaşmanın üzerinde çok az zaman geçmesi solventleri ve akıyı hapsedebilir ve lehim boşluklarının yanı sıra soğuk veya donuk bağlantı potansiyeli yaratabilir.
Soğutma bölgesi
Son bölge, işlenmiş levhayı kademeli olarak soğutmak ve lehim bağlantılarını katılaştırmak için bir soğutma bölgesidir.Uygun soğutma, aşırı intermetalik oluşumu veya bileşenlerde termal şoku engeller.Soğutma bölgesindeki tipik sıcaklıklar 30–100 °C (86–212 °F) arasındadır.Mekanik açıdan en sağlam olan ince taneli bir yapı oluşturmak için hızlı bir soğutma hızı seçilmiştir.
[1] Maksimum artış hızının aksine, yavaşlama hızı genellikle göz ardı edilir.Belirli sıcaklıkların üzerinde rampa hızı daha az kritik olabilir, ancak herhangi bir bileşen için izin verilen maksimum eğim, bileşenin ısınmasına veya soğumasına bakılmaksızın geçerli olmalıdır.Genellikle 4°C/s'lik bir soğutma hızı önerilir.Proses sonuçlarını analiz ederken dikkate alınması gereken bir parametredir.
"Yeniden akış" terimi, üzerinde katı bir lehim alaşımı kütlesinin erimesinin kesin olduğu sıcaklığı (yalnızca yumuşamanın aksine) belirtmek için kullanılır.Bu sıcaklığın altına soğutulursa lehim akmayacaktır.Bir kez daha ısıtıldığında lehim yeniden akacaktır; dolayısıyla "yeniden akacaktır".
Yeniden akışlı lehimlemeyi kullanan modern devre montaj teknikleri, lehimin birden fazla akmasına mutlaka izin vermez.Lehim pastasındaki granül lehimin, ilgili lehimin yeniden akış sıcaklığını aştığını garanti ederler.
Termal profil oluşturma
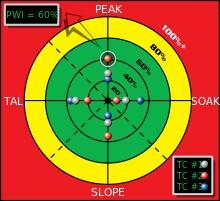
Bir termal profil için İşlem Penceresi Dizininin grafiksel temsili.
Elektronik imalat endüstrisinde, bir termal sürecin sağlamlığını ölçmek için Süreç Penceresi Endeksi (PWI) olarak bilinen istatistiksel bir ölçüm kullanılır.PWI, bir prosesin, Spesifikasyon Limiti olarak bilinen, kullanıcı tanımlı bir proses limitine ne kadar iyi "uyduğunu" ölçmeye yardımcı olur. Her termal profil, bir proses penceresine (spesifikasyon veya tolerans limiti) nasıl "uyduğuna" göre sıralanır.
İşlem penceresinin merkezi sıfır olarak tanımlanır ve işlem penceresinin en uç kenarı %99 olarak tanımlanır. %100'den büyük veya buna eşit bir PWI, profilin ürünü spesifikasyon dahilinde işlemediğini gösterir.%99'luk bir PWI, profilin ürünü spesifikasyon dahilinde işlediğini ancak süreç penceresinin kenarında çalıştığını gösterir.%60'lık bir PWI, bir profilin süreç spesifikasyonunun %60'ını kullandığını gösterir.Üreticiler, PWI değerlerini kullanarak belirli bir termal profilin proses penceresinin ne kadarını kullandığını belirleyebilir.Daha düşük bir PWI değeri daha sağlam bir profile işaret eder.
Maksimum verimlilik için, termal profilin tepe noktası, eğimi, yeniden akışı ve ıslatma işlemleri için ayrı PWI değerleri hesaplanır.Çıkışı etkileyen termal şok olasılığını önlemek için termal profildeki en dik eğim belirlenmeli ve seviyelendirilmelidir.Üreticiler eğimin dikliğini doğru bir şekilde belirlemek ve azaltmak için özel yapım yazılımlar kullanır.Ek olarak yazılım aynı zamanda zirve, eğim, yeniden akış ve ıslatma işlemleri için PWI değerlerini otomatik olarak yeniden kalibre eder.Mühendisler, PWI değerlerini ayarlayarak yeniden akışlı lehimleme işinin aşırı ısınmamasını veya çok hızlı soğumamasını sağlayabilirler.
Gönderim zamanı: Mar-01-2022