Η συγκόλληση εκ νέου ροής είναι μια διαδικασία κατά την οποία χρησιμοποιείται μια πάστα συγκόλλησης (ένα κολλώδες μείγμα κόλλησης σε σκόνη και ροής) για την προσωρινή σύνδεση ενός ή περισσότερων ηλεκτρικών εξαρτημάτων στα τακάκια επαφής τους, μετά την οποία ολόκληρο το συγκρότημα υποβάλλεται σε ελεγχόμενη θερμότητα, η οποία λιώνει τη συγκόλληση , συνδέοντας μόνιμα την άρθρωση.Η θέρμανση μπορεί να επιτευχθεί περνώντας το συγκρότημα μέσω ενός φούρνου αναρροής ή κάτω από μια λάμπα υπερύθρων ή με συγκόλληση μεμονωμένων αρμών με ένα μολύβι θερμού αέρα.
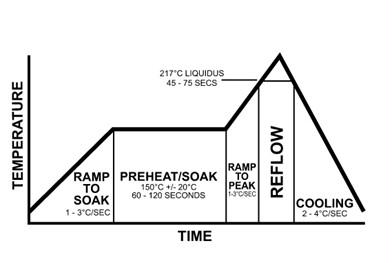
Η συγκόλληση με επαναροή είναι η πιο κοινή μέθοδος σύνδεσης εξαρτημάτων επιφανειακής βάσης σε μια πλακέτα κυκλώματος, αν και μπορεί επίσης να χρησιμοποιηθεί για εξαρτήματα διαμπερούς οπής γεμίζοντας τις οπές με πάστα συγκόλλησης και εισάγοντας τα καλώδια εξαρτημάτων μέσα από την πάστα.Επειδή η συγκόλληση κυμάτων μπορεί να είναι απλούστερη και φθηνότερη, η επαναροή δεν χρησιμοποιείται γενικά σε πλακέτες καθαρής οπής.Όταν χρησιμοποιείται σε πλακέτες που περιέχουν ένα μείγμα εξαρτημάτων SMT και THT, η επαναροή διαμπερούς οπής επιτρέπει την εξάλειψη του βήματος συγκόλλησης κυμάτων από τη διαδικασία συναρμολόγησης, μειώνοντας ενδεχομένως το κόστος συναρμολόγησης.
Ο στόχος της διαδικασίας επαναροής είναι να λιώσει η συγκόλληση και να θερμανθούν οι γειτονικές επιφάνειες, χωρίς υπερθέρμανση και ζημιά στα ηλεκτρικά εξαρτήματα.Στη συμβατική διαδικασία συγκόλλησης με επαναροή, υπάρχουν συνήθως τέσσερα στάδια, που ονομάζονται "ζώνες", το καθένα έχει ένα ξεχωριστό θερμικό προφίλ: προθέρμανση, θερμικό εμποτισμό (συχνά βραχύνεται σε απλώς εμποτισμό), επαναροή και ψύξη.
Ζώνη προθέρμανσης
Η μέγιστη κλίση είναι μια σχέση θερμοκρασίας/χρόνου που μετρά πόσο γρήγορα αλλάζει η θερμοκρασία στην πλακέτα τυπωμένου κυκλώματος.Η ζώνη προθέρμανσης είναι συχνά η μεγαλύτερη από τις ζώνες και συχνά καθορίζει τον ρυθμό ράμπας.Ο ρυθμός ανόδου είναι συνήθως κάπου μεταξύ 1,0 °C και 3,0 °C ανά δευτερόλεπτο, συχνά πέφτοντας μεταξύ 2,0 °C και 3,0 °C (4 °F έως 5 °F) ανά δευτερόλεπτο.Εάν ο ρυθμός υπερβαίνει τη μέγιστη κλίση, μπορεί να προκληθεί ζημιά στα εξαρτήματα από θερμικό σοκ ή ρωγμές.
Η πάστα συγκόλλησης μπορεί επίσης να έχει αποτέλεσμα πιτσιλίσματος.Το τμήμα προθέρμανσης είναι το σημείο όπου ο διαλύτης στην πάστα αρχίζει να εξατμίζεται και εάν ο ρυθμός ανόδου (ή το επίπεδο θερμοκρασίας) είναι πολύ χαμηλός, η εξάτμιση των πτητικών ροής είναι ατελής.
Ζώνη θερμικής εμποτισμού
Το δεύτερο τμήμα, το θερμικό εμποτισμό, είναι συνήθως μια έκθεση 60 έως 120 δευτερολέπτων για την απομάκρυνση των πτητικών της πάστας συγκόλλησης και την ενεργοποίηση των ροών (βλέπε ροή), όπου τα εξαρτήματα ροής ξεκινούν την οξείδωση στα καλώδια και τα μαξιλαράκια εξαρτημάτων.Η πολύ υψηλή θερμοκρασία μπορεί να οδηγήσει σε πιτσίλισμα ή σφαιροποίηση της κόλλησης καθώς και σε οξείδωση της πάστας, των μαξιλαριών στερέωσης και των απολήξεων των εξαρτημάτων.
Ομοίως, οι ροές μπορεί να μην ενεργοποιηθούν πλήρως εάν η θερμοκρασία είναι πολύ χαμηλή.Στο τέλος της ζώνης εμποτισμού επιθυμείται μια θερμική ισορροπία ολόκληρου του συγκροτήματος ακριβώς πριν από τη ζώνη επαναροής.Προτείνεται ένα προφίλ εμποτισμού για τη μείωση τυχόν δέλτα Τ μεταξύ εξαρτημάτων διαφορετικών μεγεθών ή εάν το συγκρότημα PCB είναι πολύ μεγάλο.Συνιστάται επίσης ένα προφίλ εμποτισμού για τη μείωση του κενού σε πακέτα τύπου διάταξης περιοχής.
Ζώνη επαναροής
Το τρίτο τμήμα, η ζώνη επαναροής, αναφέρεται επίσης ως «χρόνος πάνω από την αναρροή» ή «χρόνος πάνω από το υγρό» (TAL) και είναι το μέρος της διαδικασίας όπου επιτυγχάνεται η μέγιστη θερμοκρασία.Μια σημαντική παράμετρος είναι η μέγιστη θερμοκρασία, η οποία είναι η μέγιστη επιτρεπόμενη θερμοκρασία ολόκληρης της διαδικασίας.Μια κοινή θερμοκρασία κορυφής είναι 20–40 °C πάνω από το υγρό. Αυτό το όριο καθορίζεται από το εξάρτημα στο συγκρότημα με τη χαμηλότερη ανοχή σε υψηλές θερμοκρασίες (Το εξάρτημα που είναι πιο ευαίσθητο σε θερμική βλάβη).Μια τυπική οδηγία είναι η αφαίρεση 5 °C από τη μέγιστη θερμοκρασία που μπορεί να αντέξει το πιο ευάλωτο συστατικό για να φτάσει στη μέγιστη θερμοκρασία για τη διεργασία.Είναι σημαντικό να παρακολουθείτε τη θερμοκρασία της διαδικασίας για να μην υπερβεί αυτό το όριο.
Επιπλέον, οι υψηλές θερμοκρασίες (άνω των 260 °C) μπορεί να προκαλέσουν βλάβη στις εσωτερικές μήτρες των εξαρτημάτων SMT καθώς και να ενθαρρύνουν τη διαμεταλλική ανάπτυξη.Αντίθετα, μια θερμοκρασία που δεν είναι αρκετά καυτή μπορεί να εμποδίσει την επαρκή ροή της πάστας.
Ο χρόνος πάνω από το υγρό (TAL) ή ο χρόνος πάνω από την επαναροή, μετρά πόσο καιρό η συγκόλληση είναι υγρό.Η ροή μειώνει την επιφανειακή τάση στη συμβολή των μετάλλων για την επίτευξη μεταλλουργικής συγκόλλησης, επιτρέποντας στις επιμέρους σφαίρες σκόνης συγκόλλησης να συνδυαστούν.Εάν ο χρόνος προφίλ υπερβαίνει τις προδιαγραφές του κατασκευαστή, το αποτέλεσμα μπορεί να είναι πρόωρη ενεργοποίηση ή κατανάλωση ροής, πράγμα που «στεγνώνει» την πάστα πριν από το σχηματισμό της ένωσης συγκόλλησης.Μια ανεπαρκής σχέση χρόνου/θερμοκρασίας προκαλεί μείωση της καθαριστικής δράσης της ροής, με αποτέλεσμα κακή διαβροχή, ανεπαρκή αφαίρεση του διαλύτη και της ροής και πιθανώς ελαττωματικούς συνδέσμους συγκόλλησης.
Οι ειδικοί προτείνουν συνήθως το μικρότερο δυνατό TAL, ωστόσο, οι περισσότερες πάστες ορίζουν ένα ελάχιστο TAL 30 δευτερολέπτων, αν και δεν φαίνεται να υπάρχει σαφής λόγος για τον συγκεκριμένο χρόνο.Μια πιθανότητα είναι ότι υπάρχουν σημεία στο PCB που δεν μετρώνται κατά τη δημιουργία προφίλ, και επομένως, η ρύθμιση του ελάχιστου επιτρεπόμενου χρόνου στα 30 δευτερόλεπτα μειώνει τις πιθανότητες να μην ξαναρέει μια μη μετρημένη περιοχή.Ένας υψηλός ελάχιστος χρόνος επαναροής παρέχει επίσης ένα περιθώριο ασφάλειας έναντι των αλλαγών θερμοκρασίας του φούρνου.Ο χρόνος διαβροχής παραμένει ιδανικά κάτω από 60 δευτερόλεπτα πάνω από το υγρό.Ο επιπλέον χρόνος πάνω από το υγρό μπορεί να προκαλέσει υπερβολική διαμεταλλική ανάπτυξη, η οποία μπορεί να οδηγήσει σε ευθραυστότητα των αρθρώσεων.Η πλακέτα και τα εξαρτήματα μπορεί επίσης να καταστραφούν σε εκτεταμένους χρόνους κατά τη διάρκεια του liquidus, και τα περισσότερα εξαρτήματα έχουν ένα καλά καθορισμένο χρονικό όριο για το χρονικό διάστημα που μπορεί να εκτεθούν σε θερμοκρασίες πάνω από ένα δεδομένο μέγιστο.
Πολύ λίγος χρόνος πάνω από το υγρό μπορεί να παγιδεύσει τους διαλύτες και τη ροή και να δημιουργήσει τη δυνατότητα για ψυχρές ή θαμπές αρθρώσεις καθώς και κενά συγκόλλησης.
Ζώνη ψύξης
Η τελευταία ζώνη είναι μια ζώνη ψύξης για τη σταδιακή ψύξη της επεξεργασμένης σανίδας και τη στερεοποίηση των αρμών συγκόλλησης.Η σωστή ψύξη εμποδίζει τον υπερβολικό διαμεταλλικό σχηματισμό ή το θερμικό σοκ στα εξαρτήματα.Οι τυπικές θερμοκρασίες στη ζώνη ψύξης κυμαίνονται από 30–100 °C (86–212 °F).Επιλέγεται ένας γρήγορος ρυθμός ψύξης για τη δημιουργία μιας δομής λεπτού κόκκου που είναι πιο εύρωστη μηχανικά.
[1] Σε αντίθεση με το μέγιστο ρυθμό αύξησης, ο ρυθμός ράμπας-κάτω συχνά αγνοείται.Μπορεί ο ρυθμός ράμπας να είναι λιγότερο κρίσιμος πάνω από ορισμένες θερμοκρασίες, ωστόσο, η μέγιστη επιτρεπόμενη κλίση για οποιοδήποτε εξάρτημα θα πρέπει να ισχύει είτε το εξάρτημα θερμαίνεται είτε ψύχεται.Συνήθως προτείνεται ένας ρυθμός ψύξης 4°C/s.Είναι μια παράμετρος που πρέπει να λαμβάνεται υπόψη κατά την ανάλυση των αποτελεσμάτων της διαδικασίας.
Ο όρος "reflow" χρησιμοποιείται για να αναφέρεται στη θερμοκρασία πάνω από την οποία μια στερεή μάζα κράματος συγκόλλησης είναι βέβαιο ότι θα λιώσει (σε αντίθεση με το απλώς μαλακώσει).Εάν κρυώσει κάτω από αυτή τη θερμοκρασία, η συγκόλληση δεν θα ρέει.Η συγκόλληση θερμαίνεται για άλλη μια φορά από πάνω του, και θα ρέει ξανά - επομένως "εκ νέου ροή".
Οι σύγχρονες τεχνικές συναρμολόγησης κυκλώματος που χρησιμοποιούν συγκόλληση με επαναροή δεν επιτρέπουν απαραίτητα στη συγκόλληση να ρέει περισσότερες από μία φορές.Εγγυούνται ότι η κοκκοποιημένη συγκόλληση που περιέχεται στην πάστα συγκόλλησης ξεπερνά τη θερμοκρασία επαναροής της εμπλεκόμενης συγκόλλησης.
Θερμικό προφίλ
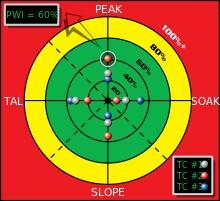
Μια γραφική αναπαράσταση του δείκτη παραθύρου διεργασίας για ένα θερμικό προφίλ.
Στη βιομηχανία παραγωγής ηλεκτρονικών, ένα στατιστικό μέτρο, γνωστό ως δείκτης παραθύρου διεργασίας (PWI) χρησιμοποιείται για να ποσοτικοποιήσει την ευρωστία μιας θερμικής διαδικασίας.Το PWI βοηθά στη μέτρηση του πόσο καλά μια διεργασία "ταιριάζει" σε ένα όριο διεργασίας που ορίζεται από το χρήστη, γνωστό ως Specification Limit. Κάθε θερμικό προφίλ κατατάσσεται ανάλογα με το πώς "ταιριάζει" σε ένα παράθυρο διεργασίας (το όριο προδιαγραφής ή ανοχής).
Το κέντρο του παραθύρου διεργασίας ορίζεται ως μηδέν και το ακραίο άκρο του παραθύρου διεργασίας ως 99%. Ένα PWI μεγαλύτερο ή ίσο με 100% υποδηλώνει ότι το προφίλ δεν επεξεργάζεται το προϊόν σύμφωνα με τις προδιαγραφές.Ένα PWI 99% υποδηλώνει ότι το προφίλ επεξεργάζεται το προϊόν σύμφωνα με τις προδιαγραφές, αλλά εκτελείται στην άκρη του παραθύρου διεργασίας.Ένα PWI 60% υποδηλώνει ότι ένα προφίλ χρησιμοποιεί το 60% των προδιαγραφών διαδικασίας.Χρησιμοποιώντας τιμές PWI, οι κατασκευαστές μπορούν να καθορίσουν πόσο από το παράθυρο διεργασίας χρησιμοποιεί ένα συγκεκριμένο θερμικό προφίλ.Μια χαμηλότερη τιμή PWI υποδηλώνει ένα πιο στιβαρό προφίλ.
Για μέγιστη απόδοση, υπολογίζονται ξεχωριστές τιμές PWI για διεργασίες κορυφής, κλίσης, αναρροής και εμποτισμού ενός θερμικού προφίλ.Για να αποφευχθεί η πιθανότητα θερμικού σοκ να επηρεάσει την έξοδο, πρέπει να προσδιοριστεί και να ισοπεδωθεί η πιο απότομη κλίση στο θερμικό προφίλ.Οι κατασκευαστές χρησιμοποιούν προσαρμοσμένο λογισμικό για να προσδιορίσουν με ακρίβεια και να μειώσουν την απότομη κλίση της κλίσης.Επιπλέον, το λογισμικό επαναβαθμονομεί επίσης αυτόματα τις τιμές PWI για τις διεργασίες κορυφής, κλίσης, επαναροής και εμποτισμού.Ορίζοντας τιμές PWI, οι μηχανικοί μπορούν να διασφαλίσουν ότι η εργασία συγκόλλησης με επαναροή δεν υπερθερμαίνεται ή ψύχεται πολύ γρήγορα.
Ώρα δημοσίευσης: Mar-01-2022